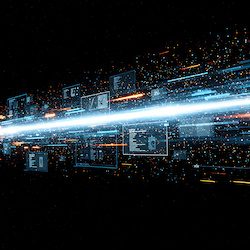
Q&A with Dhananjay Patil
The latest trends in artificial intelligence (AI), data centers, avionics, and medical devices demand extremely high-speed data processing due to the rise in computational processing. As consumers appreciate the benefits of faster generative AIs, the demand for speed is expected to grow multifold.
Fast data flow between components calls for fresh approaches for manufacturing, signal integrity, and power delivery. As data rates rise, it is imperative for engineers to strike a balance between cost, complexity, and performance.
As a lead hardware design engineer with 25 years of experience and currently working for FAANG company, Dhananjay Patil has designed and developed high-speed boards and knows avionics, medical equipment, networking, and consumer electronics intrinsically. Patil shares his expertise in this interview on innovative ideas reshaping printed circuit board (PCB) design.
Q: As data rates rise and high-speed interfaces evolve, what challenges do engineers face?
Patil: Data transfer speeds have risen considerably over the past five to 10 years. From Gen 3, which ran at 8 gigabits per second (Gbps), the protocols have progressed to Gen 6, which enables 64 Gbps, known as the PCI Express (PCIe). Likewise, memory technology has advanced from double data rate 3 (DDR3) to DDR5, with clock rates growing from 1066 MHz to more than 4800 MHz.
As data rates climb, maintaining signal integrity gets more challenging since high-speed transmissions are more likely to create crosstalk, reflections, and distortions. The complexity of multilayer PCB designs makes the approach even more challenging. It’s crucial to consider the trade-off between performance and cost carefully since using modern materials and techniques might significantly affect the design cost.
Q: What is the role of controlled impedance in ensuring signal integrity, and how is it achieved?
Patil: Controlled impedance is the first critical factor in high-speed PCB design. It ensures the signal path has a consistent impedance from the source to the destination, minimizing signal distortions. When impedance is not properly controlled, discontinuities cause reflections, signal integrity issues and data errors. This is particularly problematic at higher data rates, where even small mismatches can impact performance.
Achieving controlled impedance involves careful selection of PCB materials, trace lengths matching, and PCB layer stackup configurations (including copper thickness change). Engineers use high-frequency dielectric materials like Rogers for critical signal layers, while more cost-effective FR-4 material is used for power and ground layers. In addition, advanced vertical interconnect access (via) techniques, such as back-drilling and laser vias, help eliminate stubs that act as antennas, causing signal reflections.
Q: How do hybrid stackups and advanced techniques impact performance and cost in PCB design?
Patil: Hybrid stackups balance high-performance materials with cost-effective solutions. Hybrid stackups enhance PCB performance by optimizing signal integrity, power delivery, and thermal management through a mix of high-performance and low-cost PCB fabrication materials. They improve reliability by reducing insertion loss, impedance mismatches, and mechanical warping.
Advanced via techniques, such as back-drilling, buried, blind, and laser vias, are important. Vias improve signal integrity, back-drilling is more affordable, while laser vias offer better precision at a higher cost.
Q: What design practices help minimize crosstalk and electromagnetic interference (EMI) in high-speed PCBs?
Patil: Minimizing crosstalk and EMI requires a combination of routing techniques and careful layout design. Differential pair routing is one of the most effective methods for reducing noise. By transmitting the same signal along two parallel traces with opposite polarities, noise that affects one trace is canceled out by the opposite signal on the other trace.
Another vital practice is shielding critical traces with ground paths. Ground planes act as barriers that contain electromagnetic fields, preventing them from affecting other components. Ensuring proper return paths for signals is equally essential to avoid unintended interference. Low-impedance power planes help reduce noise and improve system stability.
Q: Can you share a real-world project demonstrating these advanced design techniques?
Patil: One of my projects involved designing a 400-gigabit Ethernet card, with each channel handling 100-gigabit Ethernet. The layout used differential pair routing to manage the high data rates, ensuring signal integrity across layers. The card’s performance was validated using metrics like signal-to-noise ratio and eye diagram analysis to ensure clear, reliable signal transmission. This design involved 16 layers of PCB, and the final card has been successfully deployed for high-speed networking applications in data centers.
Q: How do engineers measure the success of high-speed PCB designs, and what key metrics are used?
Patil: Measuring the success of a high-speed PCB design involves evaluating several key performance indicators (KPIs) to ensure that the board performs as intended. The most used metrics include SNR, simultaneous switching noise (SSN), insertion loss, return loss, and eye diagram analysis. These metrics provide a comprehensive view of the board’s signal integrity.
SNR measures the clarity of the signal compared to background noise, while insertion loss indicates how much signal strength is lost as it travels through the PCB. Return loss measures how much signal is reflected toward the source due to impedance mismatches. Eye diagram analysis, one of the most critical tests, visually displays the quality of a differential signal. The “eye” in the diagram should be wide open—a closed eye indicates signal degradation caused by noise, reflections, or crosstalk.
These metrics are measured in simulations during the design phase and on physical boards after fabrication. Identifying and addressing issues early helps avoid costly post-production fixes and ensures reliable performance in real-world applications.
Q: What trends and innovations are shaping the future of high-speed PCB design?
Patil: One of the most significant trends is the increasing use of AI-driven design tools. These tools alter how PCBs are designed by automating routing and error detection tasks. AI tools can simulate various scenarios and optimize designs for performance and manufacturability, reducing the risk of costly errors later in the process.
Another exciting innovation is the development of photonic interconnects, in which light transmits signals instead of electrical currents. These interconnects offer the potential to reduce signal interference and drastically increase data transfer speeds. Although still in the research phase, this technology could revolutionize PCB design in the coming years.
New materials and manufacturing processes are continuously being developed to support these advancements. Visualization and cross-functional tools are available to check and ensure that PCBs, components, wires, and heatsinks live in sync with their plastics and metal enclosures.
The Road Ahead
High-speed PCB design is at the heart of modern technology, supporting the rapid data transfer rates required by AI and other data-intensive applications. As data rates rise, addressing signal integrity, power integrity, and manufacturability will remain critical challenges for engineers.
Innovations in controlled impedance routing, hybrid stackups, and advanced via techniques improve performance, while AI-driven tools and photonic interconnects promise to shape the future of PCB design. By balancing performance and cost, engineers can create designs that meet today’s technology demands while preparing for tomorrow’s challenges.
About the Author
Paul Chaney is a seasoned writer, editor, and content strategist who helps businesses craft compelling, ethical marketing narratives through his consultancy, Prescriptive Writing. With a focus on clarity, authenticity, and responsible communication, Paul empowers organizations to tell their stories with purpose and precision. Connect with him on LinkedIn.
Disclaimer: The author is completely responsible for the content of this article. The opinions expressed are their own and do not represent IEEE’s position nor that of the Computer Society nor its Leadership.